Case study: cutting costs and maximising efficiency in bulk liquid transportation
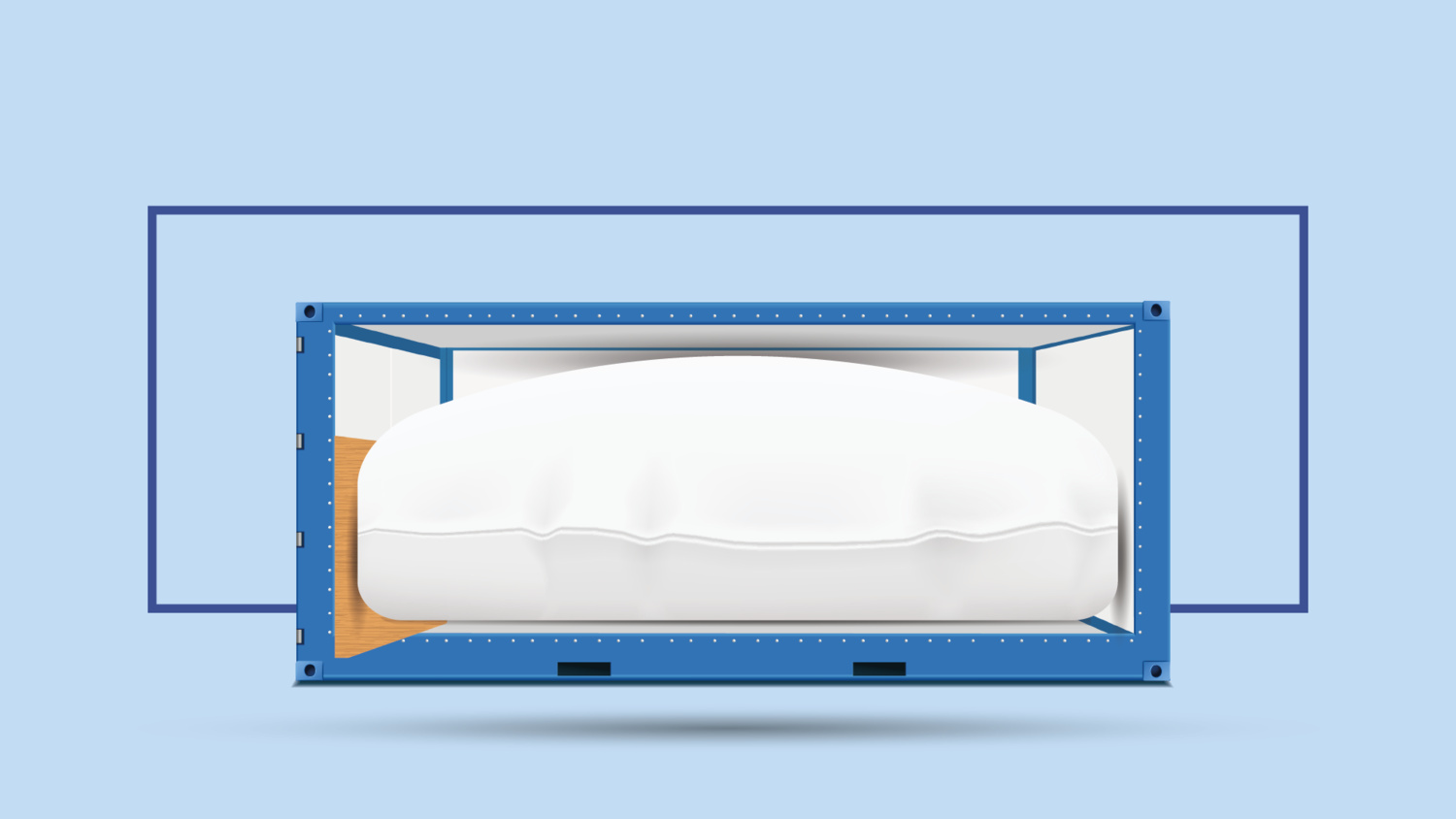
Efficiently shipping bulk liquids and maximising payload capacity presents a complex challenge, often complicated by safety concerns and logistical hurdles that lead to operational delays. Striving for cost-effectiveness while minimising environmental impact adds another layer of difficulty.
Recognising these challenges,one of the world's leading multinational consumer goods companies worked with AELER to adopt the cutting-edge Unit One container equipped with flexitanks. This innovative solution aimed to streamline the transportation of bulk detergent on their UK to Türkiye trade route, enhancing both efficiency and sustainability.
Objectives
In working with AELER, the company aimed to achieve several goals:
- Efficiency: Increase Vehicle Fill Rate (VFR)
- Cost: Reduce the cost per ton (or per unit) of cargo transported
- Sustainability:
- Reduce supply chain emissions from priority categories by 40% per unit of production by 2030, compared to the 2020 baseline
- Reduce the use of virgin petroleum plastic in priority categories by 50% by 2030, compared to the 2017 baseline
- Quality: Maintain product stability and quality while enhancing operational efficiency and sustainability
- Visibility: Enhance cargo and shipment monitoring with actionable insights
Key outcomes
Reducing cost per ton of cargo transported by up to 10%
.jpeg)
AELER containers, made from advanced composite materials, are significantly stronger than standard steel containers, allowing for a safe increase in maximum transportable payload by up to 4 tons of bulk liquid. In contrast, traditional steel containers often deform and bulge when filled to the maximum capacity of liquid, compromising safety and transport efficiency
Therefore, by transitioning to the AELER Unit One, the company successfully transported 27 tons of bulk liquid cargo per shipment, boosting the Vehicle Fill Rate (VFR) by 12.5% in the summer and 17% during the winter. This increase in payload capacity resulted in a 5-10% reduction in cost per ton of liquid transported and significantly reduced the operational load.
Eliminating single-use plastic insulation
The company successfully eliminated the use of single-use polyisocyanurate (plastic foam) insulation to protect their bulk liquid cargo in transit. By leveraging the native insulation capabilities of AELER’s advanced composite walls, the company is projected to save over 17.5 tons of single-use plastic from going to landfills in 2024.
External temperatures can drop below 0 degrees Celsius during winter months, compromising cargo integrity. Standard steel containers are traditionally lined with plastic foam sheets (PIR insulation) to protect temperature-sensitive cargo. However, these plastic sheets are single-use and inefficient to recycle, resulting in a significant environmental burden.
In contrast, the advanced composites forming the structure of AELER’s Unit One are made from recycled materials and provide insulation without requiring additional fittings. AELER’s native insulation is comparable to that of a non-operating reefer, eliminating the need for over 100 kg of plastic insulation per shipment when transporting temperature-sensitive cargo.
Real-time monitoring and total visibility
The company leveraged Control Tower, AELER’s proprietary visibility platform, to monitor its shipments in real time. Control Tower enables comprehensive container monitoring throughout the journey, displaying critical data gathered from built-in IoT devices such as GPS location, temperature, and humidity. It also provides contextual visibility directly from the shipping lines regarding ETAs and any disruptions.
Additional benefits: internal temperature control and quality of goods
The transition to AELER's Unit One containers has also enhanced cargo temperature maintenance compared to steel containers, keeping detergent temperatures above 20°C throughout the journey. This improvement is due to the Unit One’s native insulation, which is not present in steel containers. Limited variations are crucial for preserving the chemical integrity of detergents.
Additionally, the company in Turkey reported that the goods received consistently meet expected quality standards, confirming the effectiveness of these logistical improvements in maintaining product quality.
Expanding horizons: the ongoing journey
The company’s switch to AELER's Unit One containers for bulk liquid cargo on the UK to Türkiye trade route significantly boosted logistical efficiency and sustainability, underscoring the potential of innovative logistics solutions. By leveraging AELER's solution, which minimises the need for additional manpower and materials to reinforce standard dry containers, trust in utilising the flexitank option has been fostered. This enhances payload capacity, reduces CO2 emissions, and maintains product quality, showcasing the multifaceted benefits of embracing such advancements in the industry.
Building on the success of the UK-to-Türkiye trade route, the company is now strategically planning to extend the use of AELER's containers to several additional key trade routes. This decision underscores their confidence in AELER's ability to meet critical safety and cost-effectiveness needs in transporting bulk liquids. It also reaffirms the company’s commitment to sustainability, as they aim to replicate the environmental benefits and operational efficiency gains in this new trade lane.
Related resources
.jpg)
.jpg)
Setting new standards in bulk liquid transport with flexitanks
Setting new standards in bulk liquid transport with flexitanks
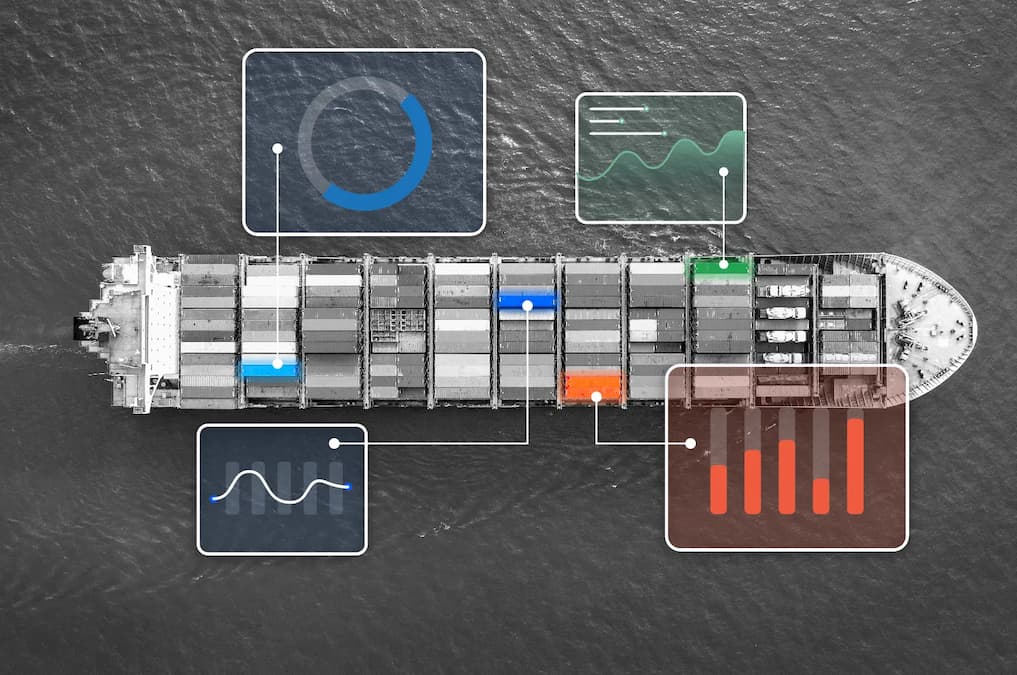
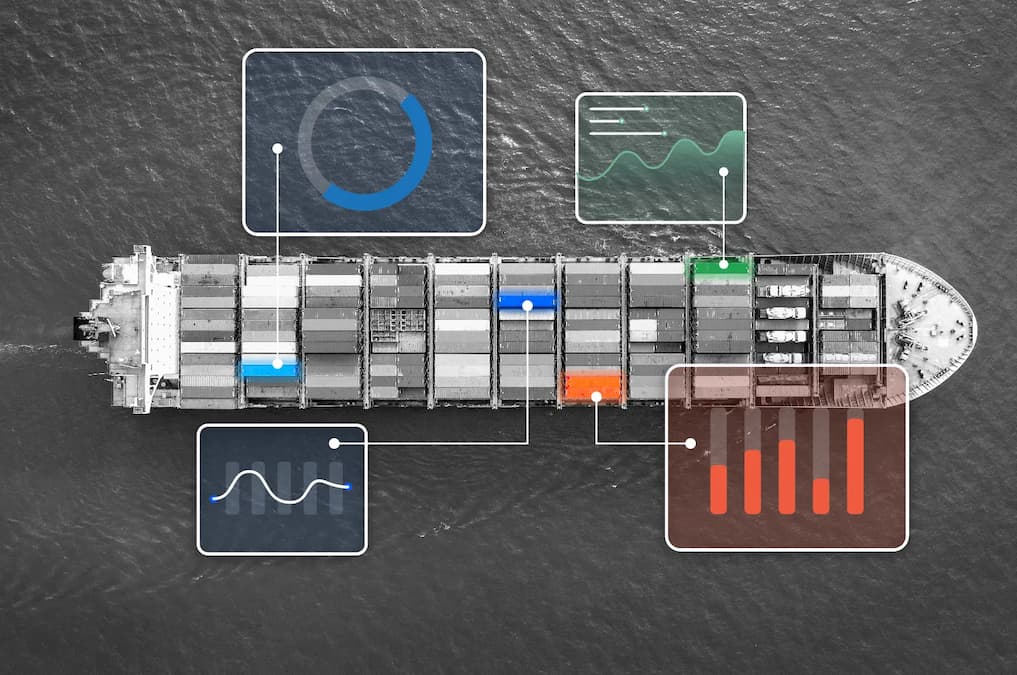
Smart containers: a comprehensive guide to the future of shipping
Smart containers: a comprehensive guide to the future of shipping
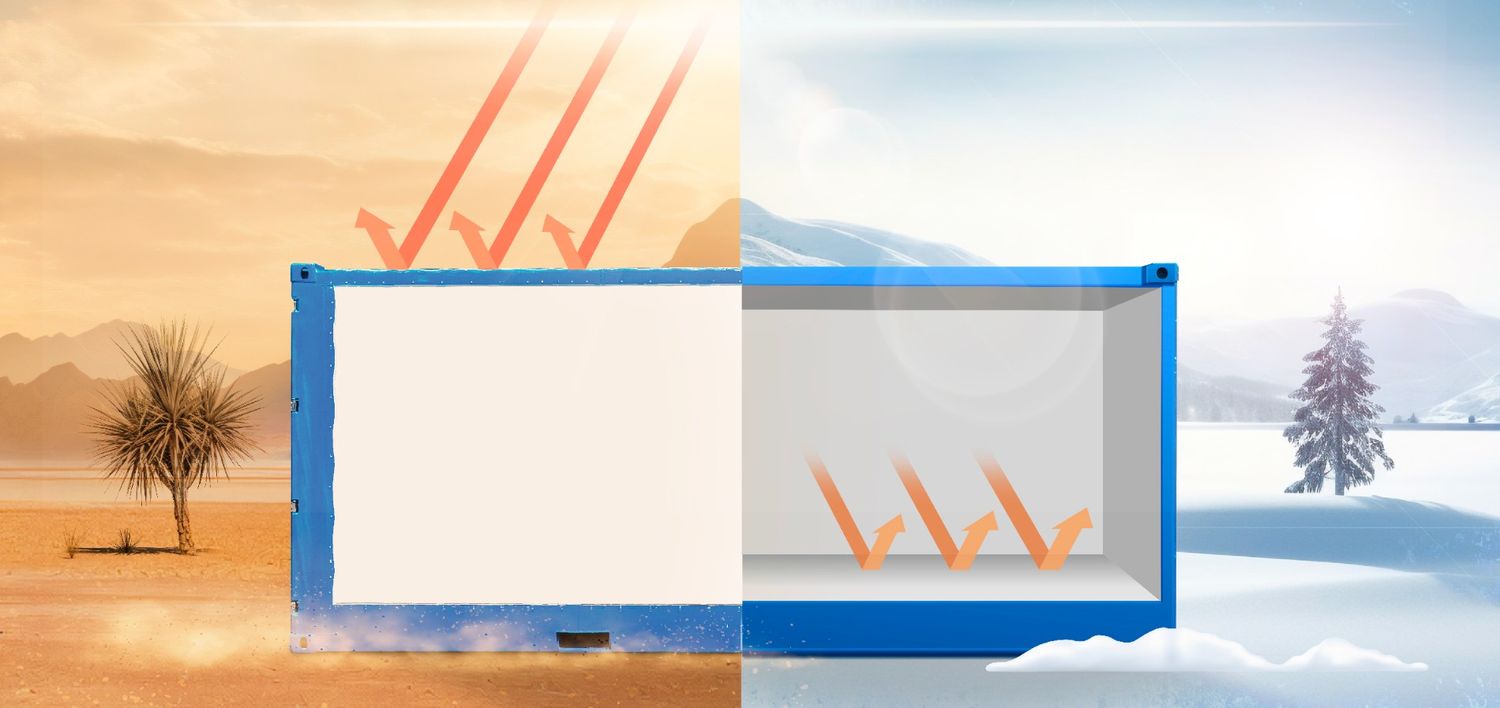
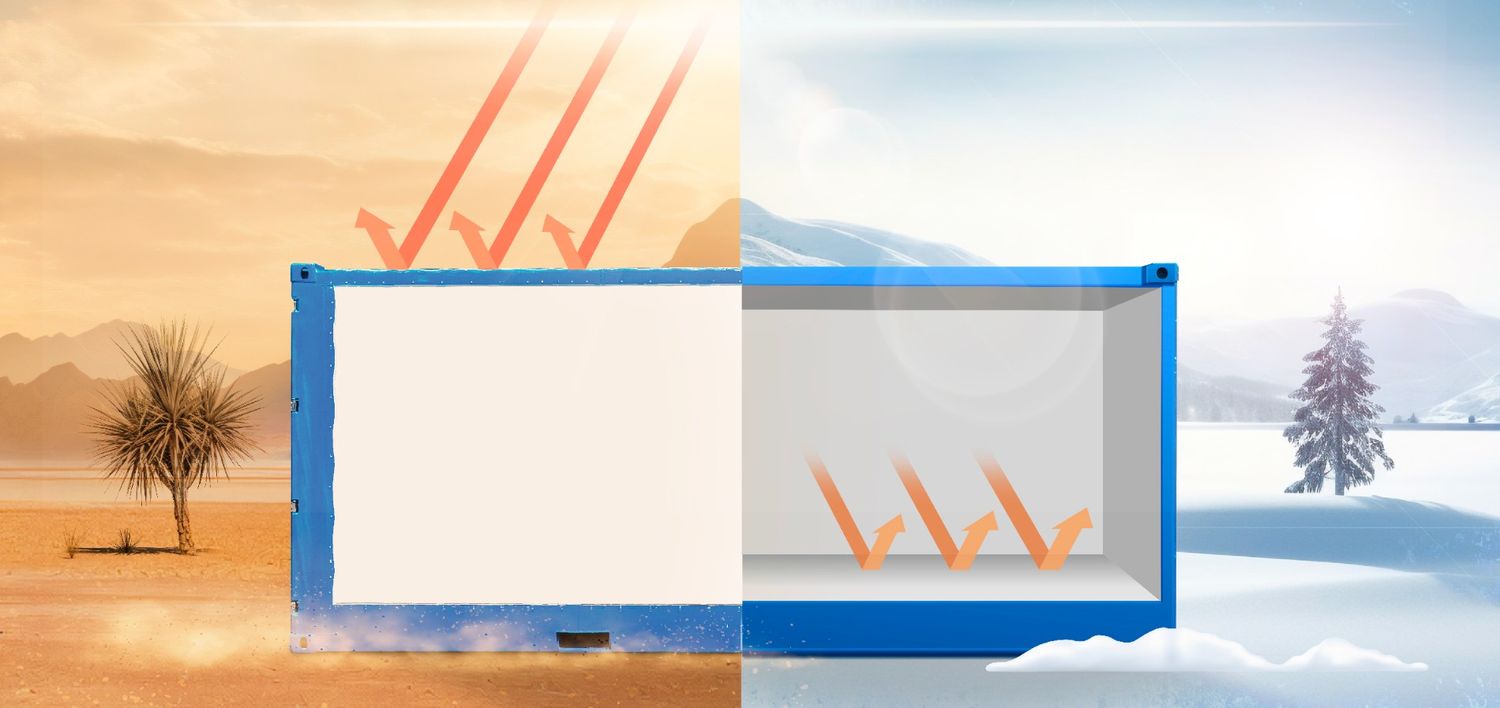