Optimising lubricant logistics with flexibag transport
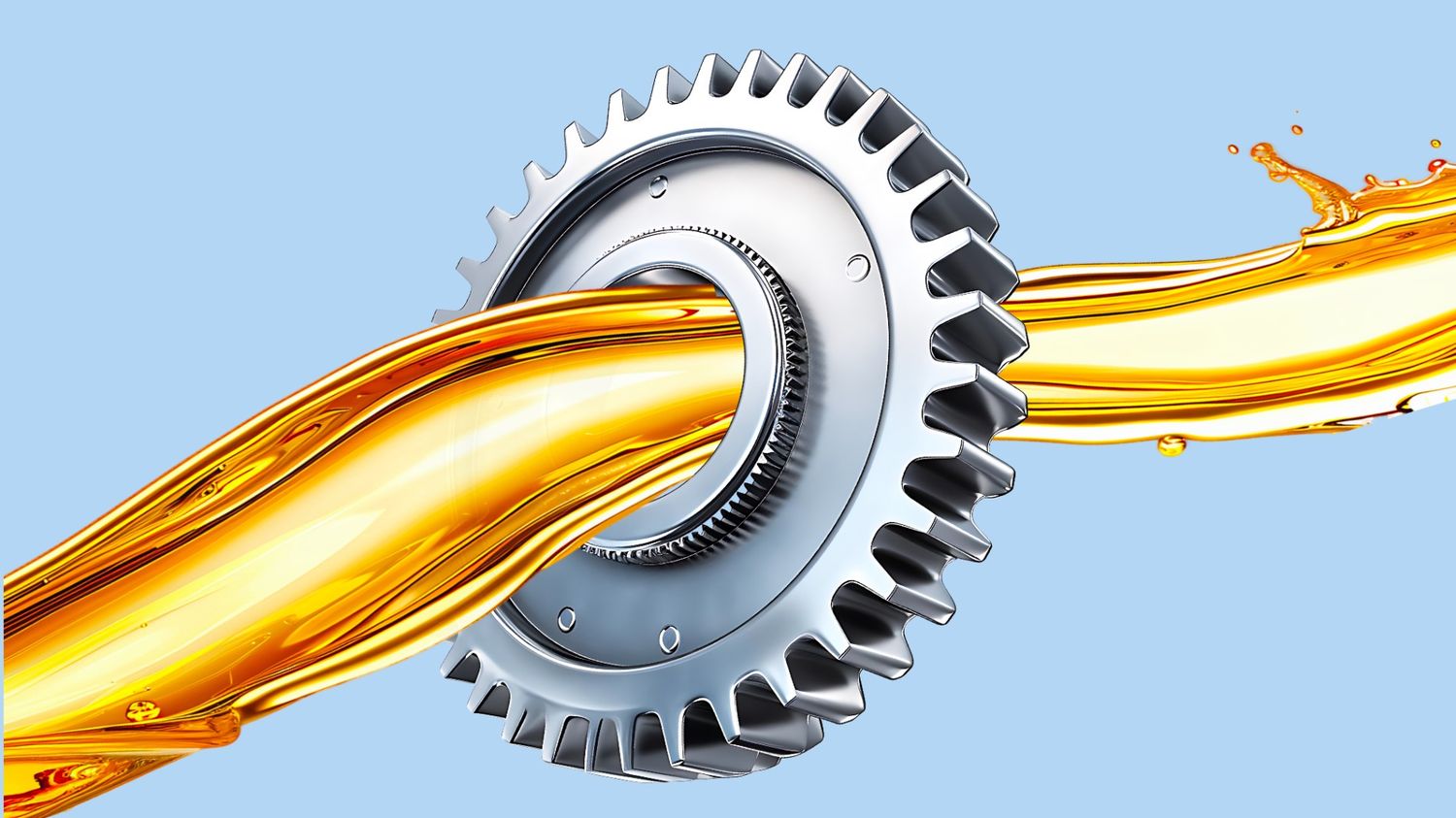
Lubricants are the lifeblood of countless industries, serving purposes that range from reducing friction and ensuring the smooth operation of machinery to enhancing the texture, performance, and longevity of cosmetic products.
Transporting lubricants efficiently and safely requires reliable methods to maintain their quality and integrity. While solutions like flexitanks and ISO tanks have served the industry for years, they have limitations that can affect overall efficiency and cost.
Therefore, a new approach is essential. By adopting a more robust container solution, the industry can achieve greater efficiency, addressing both cost and time challenges while meeting the demands of modern lubricant transport.
Transporting lubricants
The transportation of lubricants requires careful consideration of the type, volume, and destination. Due to their density and viscosity, lubricants may often harden during transport, making reheating before unloading necessary to ensure a smooth transfer to their final storage or application point. Two primary methods are commonly employed to ensure that these substances arrive at their destination in optimal condition: flexitanks and ISO tanks.
Flexitanks: maximising efficiency and sustainability in bulk lubricant transport
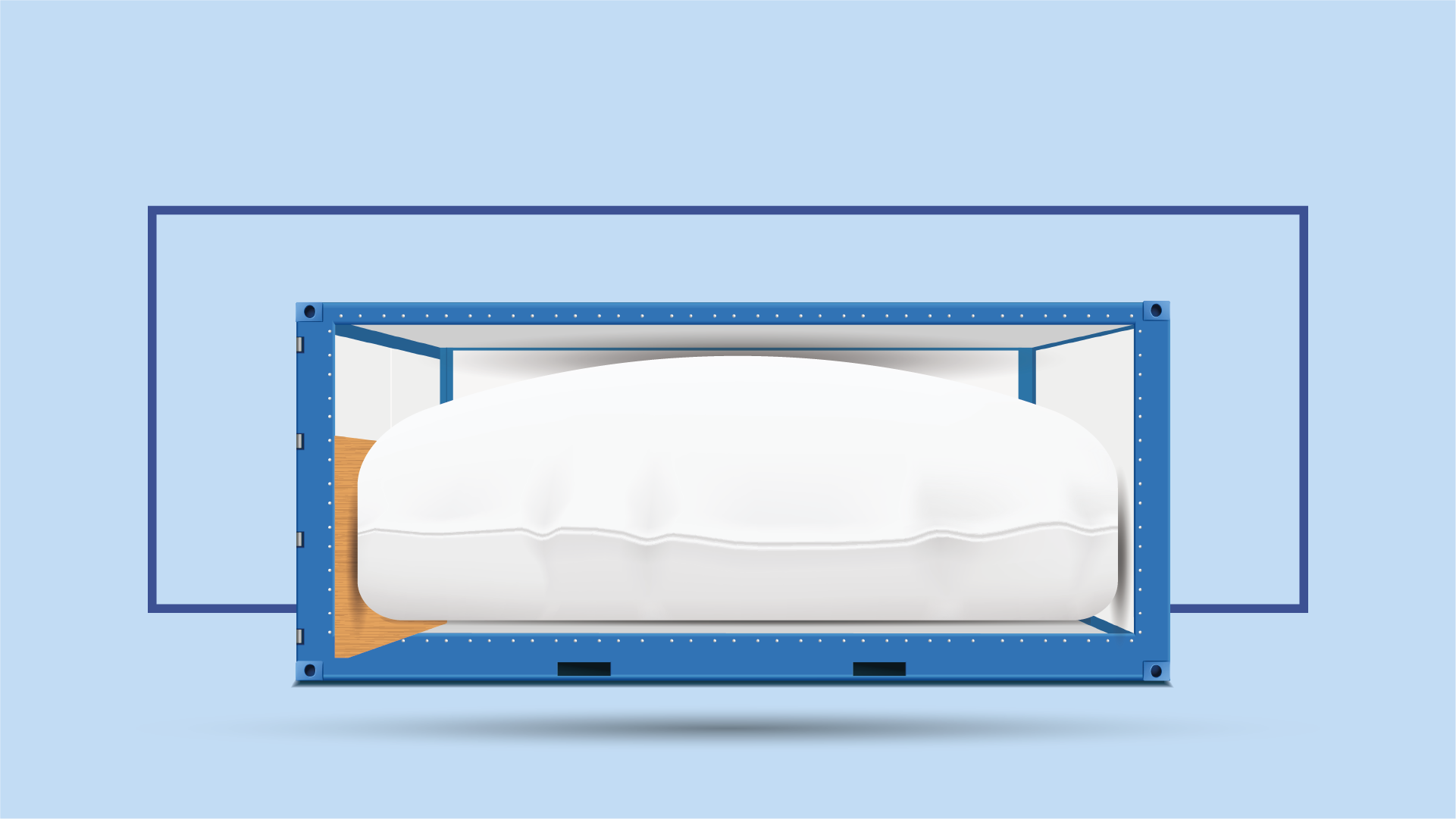
Flexitanks – large flexible bags made from polyethylene – offer an innovative solution for transporting lubricants in bulk. These tanks fit securely inside standard 20-foot dry-box containers, maximising space utilisation while ensuring safe containment during transit.
Operators use flexitanks to transport non-hazardous lubricants such as base oils, which are the raw materials for producing finished lubricants. They are also employed for certain motor oils, industrial lubricants, hydraulic fluids, and vegetable oils, the latter being biodegradable and environmentally friendly alternatives.
The key advantage of flexitanks is their ability to transport large volumes of lubricants efficiently and cost-effectively. When paired with an AELER container, flexitanks can hold up to 28 tonnes of liquid, saving cargo space and reducing costs. Additionally, the increased capacity leads to fewer shipments, lowering the environmental impact of the industry. In fact, studies indicate that flexitanks can reduce carbon emissions by up to 40%, equivalent to approximately two kilograms of CO2 per kilometre travelled.
ISO Tanks: safe and reliable transport for lubricants
ISO tanks are stainless steel cylindrical containers encased in a protective frame, standardised by the International Organization for Standardization. These tanks are used for transporting hazardous lubricants, such as certain synthetic oils used in high-performance engines or high-temperature oils used in industrial machinery that require stringent safety and quality controls. However, operators also often use ISO tanks for transporting non-hazardous lubricants, depending on availability.
ISO tanks provide numerous advantages, starting with their ability to minimise the risk of cargo damage. Their durable stainless steel construction ensures that goods are protected from damage, contamination, corrosion, and harsh weather conditions. These tanks are also designed for ease of handling, requiring minimal effort from operators during loading and unloading. Furthermore, their insulating protective layer helps to regulate product temperature by reducing the impact of external heat, allowing for temperature control during transport when necessary.
The AELER solution
Transporting lubricants requires a strong focus on both safety and efficiency. When paired with flexitanks, the AELER Unit One container - an ISO standard 20ft container - offers an innovative solution that overcomes some of the challenges associated with this method of transport.
Maximising flexitanks payloads: up to 28 tons per unit
One of the main challenges with using flexitanks in traditional steel containers is the restriction on payload capacity. Typically, flexitanks can only be loaded to a maximum of 24 tons before the sidewalls of the container begin to bulge.
In contrast, the AELER Unit One is constructed from composite materials 65% stronger than traditional steel, allowing operators to load up to 28 tons of lubricant into flexitanks without risking the container's structural integrity. This increased payload capacity reduces the number of containers needed per shipment, lowering transportation costs and improving overall efficiency and profitability.
Native insulation reducing reheating costs
Unlike steel containers requiring additional insulation, the AELER Unit One comes with natively insulated, built-in insulation, which makes the container three times more effective at maintaining temperature than standard steel containers.
This enhanced insulation is crucial for transporting lubricants as it helps maintain them at a higher temperature throughout the journey, minimising the need for reheating upon arrival. This preserves the quality of the lubricants and reduces the energy costs associated with reheating, making the AELER Unit One a cost-effective and efficient solution.
A more efficient alternative to ISO tanks
For the transport of non-hazardous lubricants, the AELER Unit One container, paired with flexitanks, presents a highly efficient alternative to ISO tanks.
One of the primary advantages is the ability to increase payload. With the AELER Unit One, operators can transport up to 28 tons of lubricant—three tons more than what ISO tanks allow. This higher payload reduces the number of containers needed per shipment, which in turn lowers transportation costs and boosts profitability.
In addition to carrying more product, AELER containers also minimise residual product loss. ISO tanks typically leave behind around 500 kg of product after unloading, resulting in a loss of approximately $600 per shipment. In contrast, the AELER Unit One, when used with flexitanks, reduces this residual product loss to a maximum of 100kg, saving around $480 per shipment.
Moreover, AELER containers deliver significant savings on reheating and cleaning costs. Thanks to their native insulation, AELER containers can maintain higher internal temperatures, reducing the need for reheating by up to 50% compared to ISO tanks. This not only cuts energy costs but also preserves the quality of the lubricants.
Simulations
To demonstrate the effectiveness of the AELER Unit One in transporting lubricants, the team undertook two simulations, each comparing the three following containers transporting lubricants in flexitanks:
- The AELER Unit One
- A standard steel container
- A standard steel container with single-use insulation
Simulation 1
- Lubricant type: Multi-purpose grease
- Cargo density kg/m3: 1000
- Cargo heat capacity J/kg/K: 2349
- Cargo temperature: 20°C
- Route: Germany to Singapore (from 1°C to 30°C)
- Season: winter
Simulation 2
- Lubricant type: Multi-purpose grease
- Cargo density kg/m3: 1000
- Cargo heat capacity J/kg/K: 2349
- Cargo temperature: 20°C
- Route: Germany to the USA (from 1°C to 4°C)
- Season: winter
Simulation results
In the first simulation, the AELER Unit One maintains a similar temperature as the insulated steel container, with the added benefits of increased payload and not requiring expensive and damaging single-use plastic insulation.
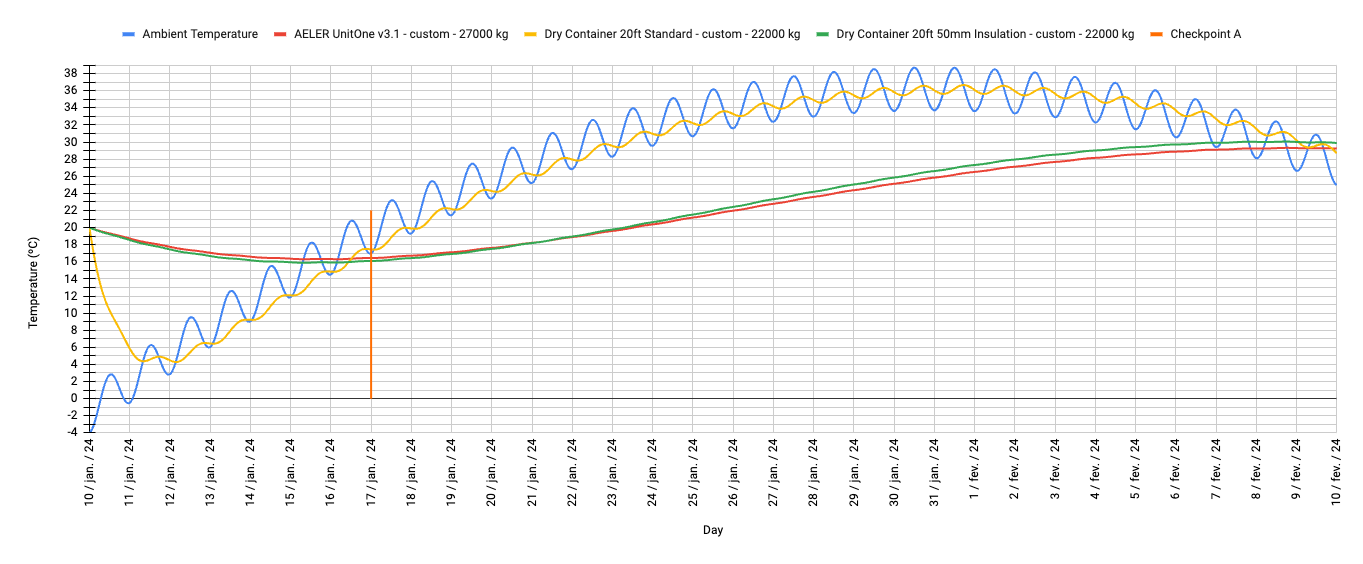
In the second simulation, the AELER Unit One keeps the lubricant two to three degrees warmer than the insulated steel container, reducing reheating costs on arrival while offering the benefits of increased payload and removing the use of single-use plastic insulation.
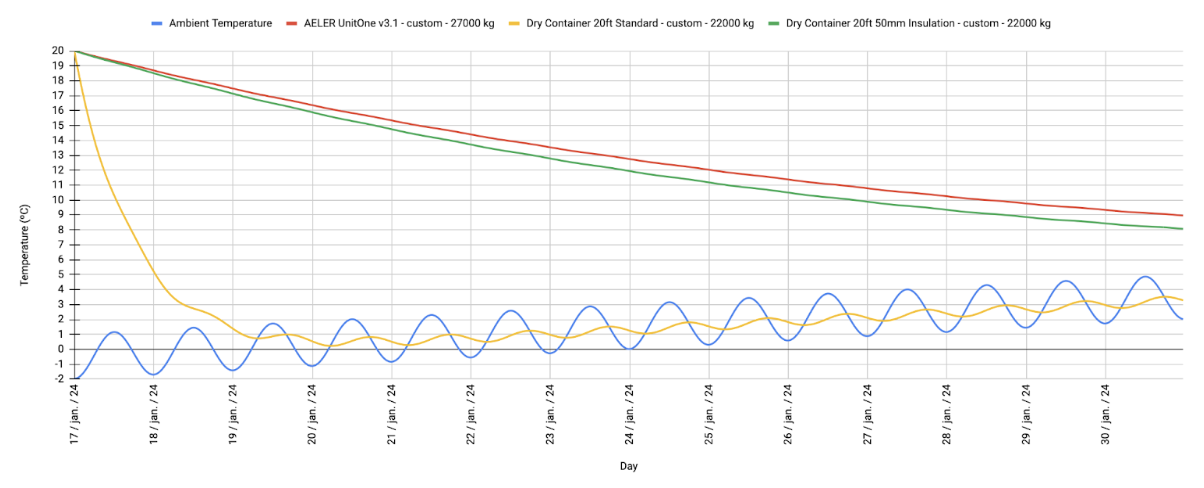
Conclusion: a smart approach to lubricant transport
Transporting lubricants presents unique challenges, from maintaining consistent temperatures to maximising payload capacity. Addressing these issues requires innovative solutions beyond traditional steel containers or ISO tanks. An improved container design with higher payload capacities and native insulation offers promising ways to enhance efficiency and reduce costs.
By maintaining consistent temperatures throughout transit and minimising the need for reheating, choosing the AELER Unit One provides tangible benefits for optimising lubricant transportation processes. As the industry evolves, embracing such innovations will be key to overcoming existing challenges and improving overall logistics efficiency.
Curious how this solution can optimise your lubricant shipments? Get in touch to find out how the AELER Unit One container can streamline your lubricant shipments and reduce costs.
Related resources
.jpg)
.jpg)
Setting new standards in bulk liquid transport with flexitanks
Setting new standards in bulk liquid transport with flexitanks
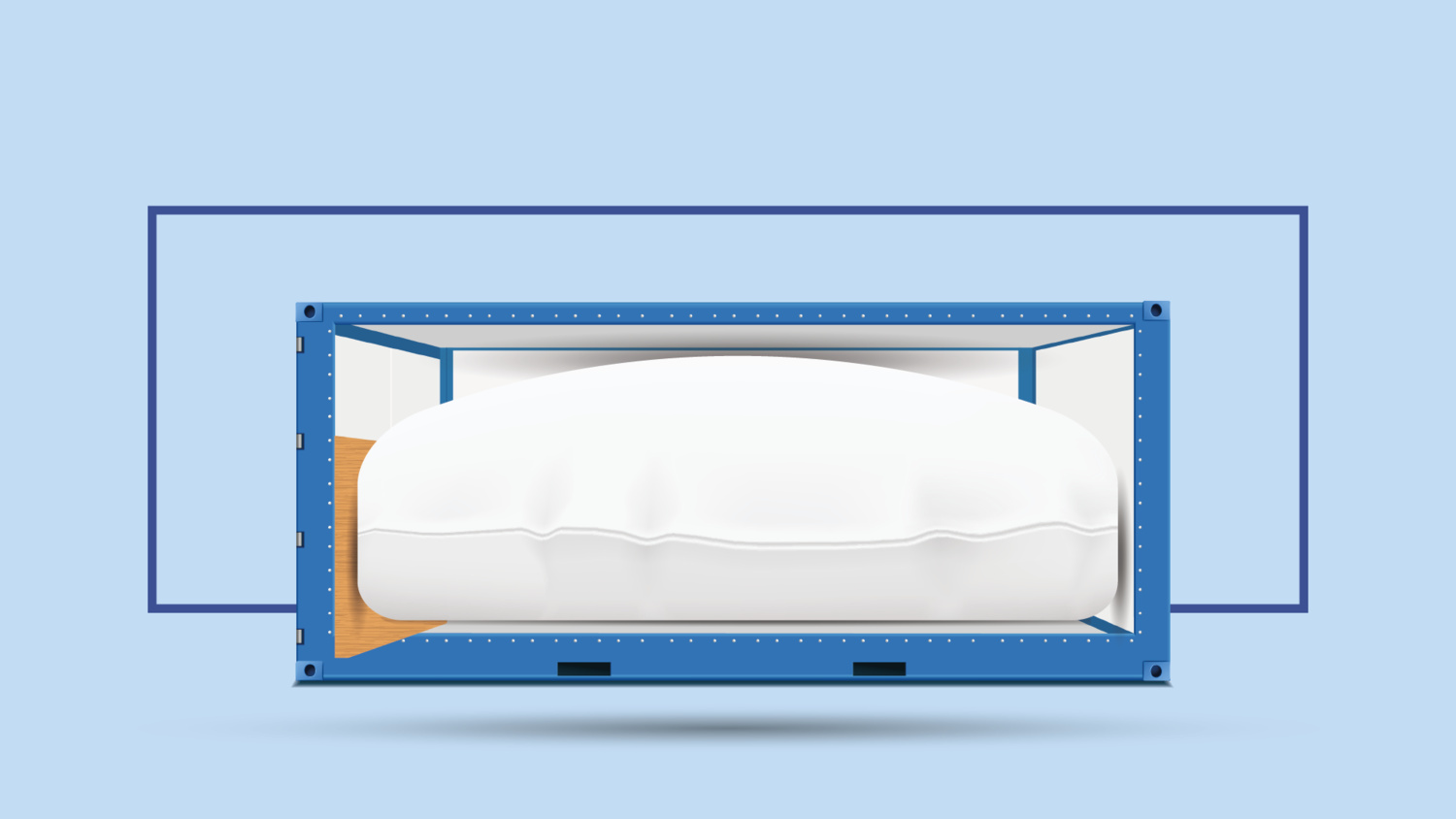
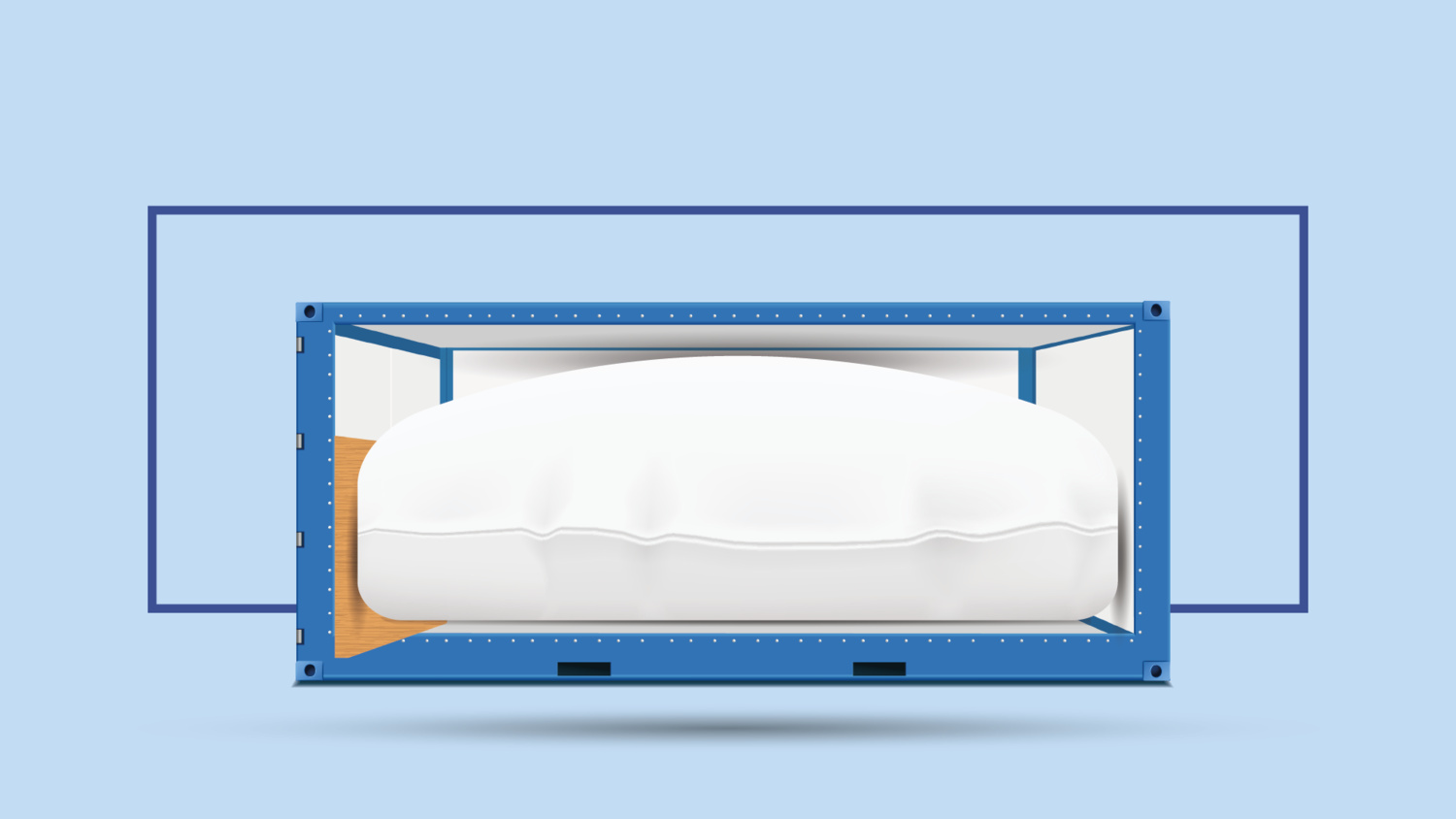
Case study: cutting costs and maximising efficiency in bulk liquid transportation
Case study: cutting costs and maximising efficiency in bulk liquid transportation
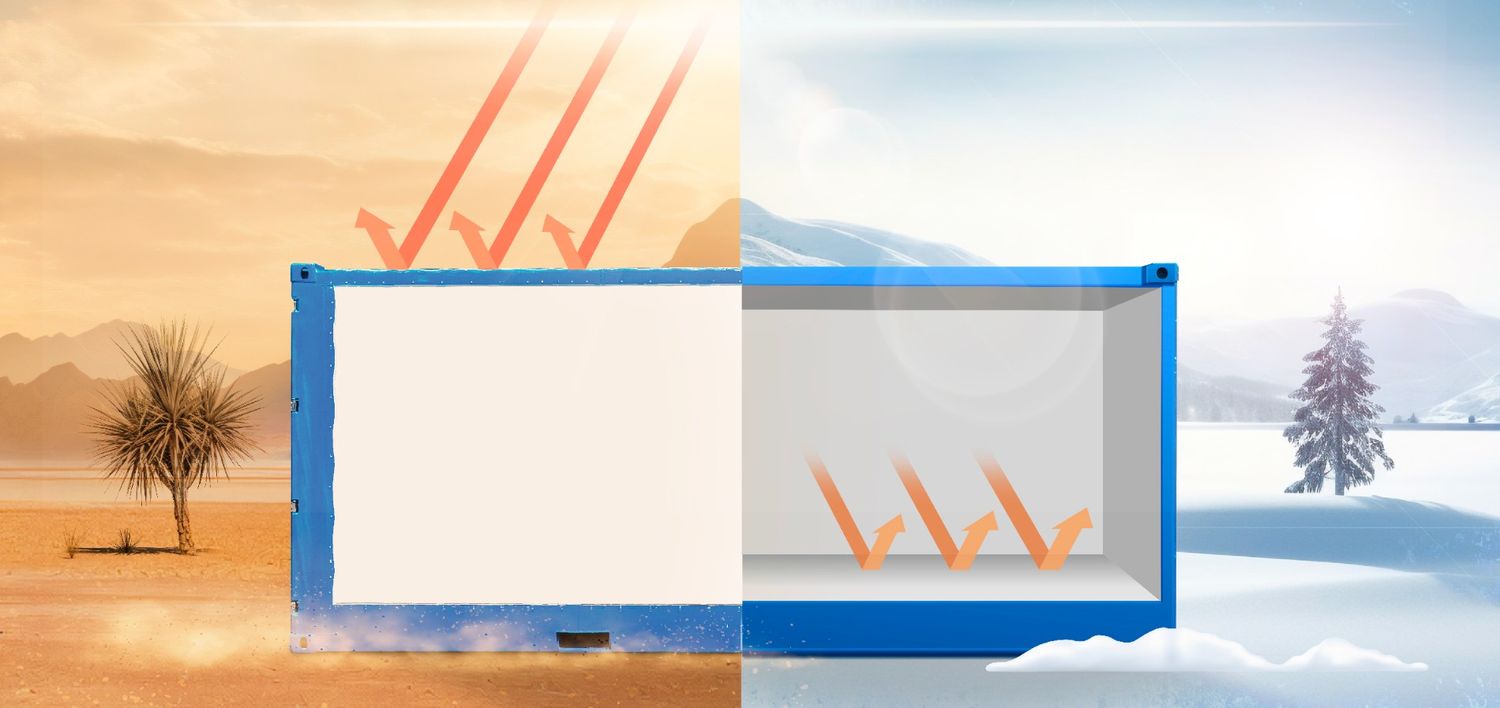
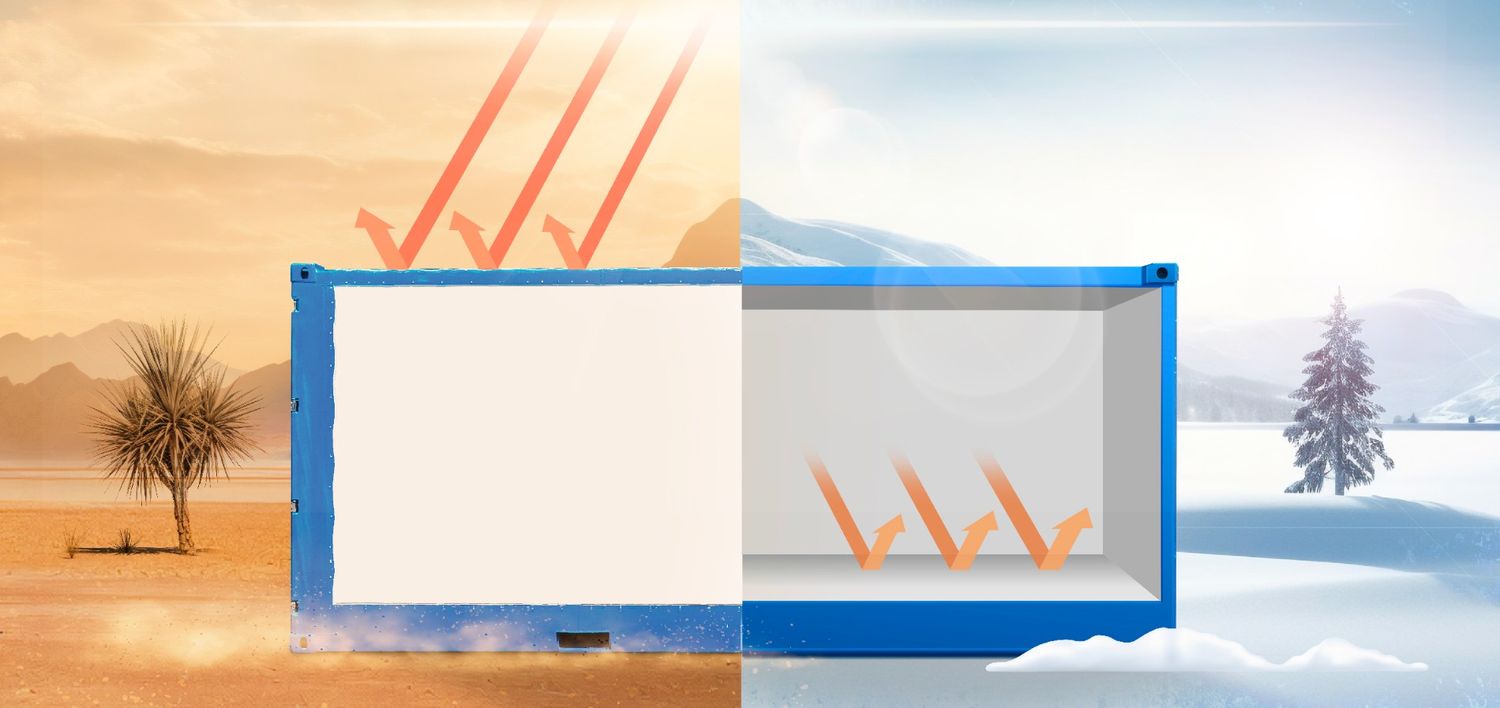