Case study: Optimising beverage transport with real-time cargo monitoring
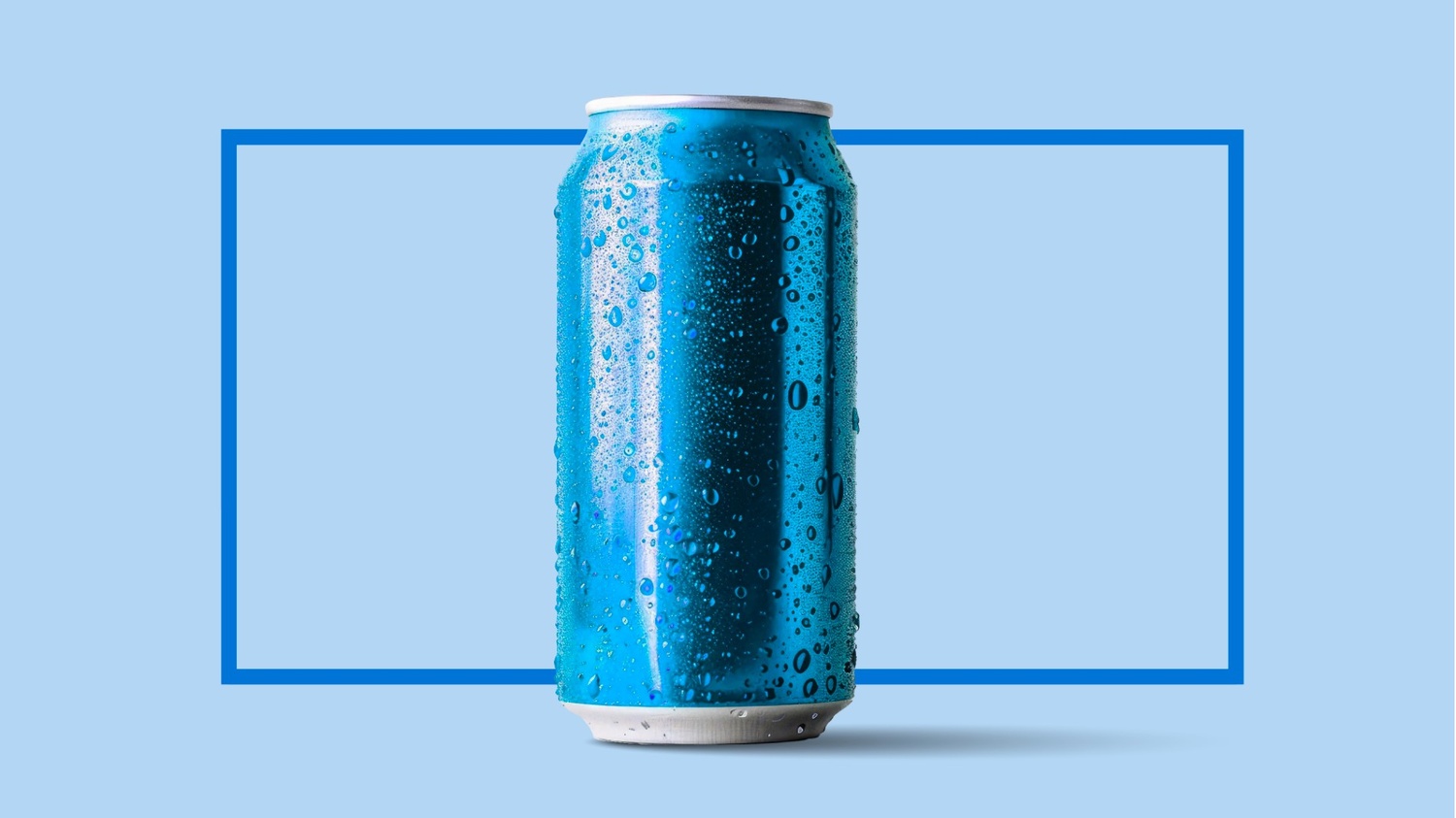
When a global leader in the food and beverage industry faced the challenge of shipping temperature and humidity-sensitive beverages across diverse geographical regions in Asia, they saw not just a logistical hurdle, but an opportunity to improve the protection and monitoring of their cargo.
With strict temperature thresholds that had to be met to ensure product integrity and a growing demand for instant, real-time data, the company sought a logistics solution that could offer both enhanced cargo protection and reliable, real-time monitoring, without increasing prices.
Maintaining product quality in challenging conditions
Transporting beverages over long distances comes with particular challenges, especially on routes where temperature fluctuations are inevitable. The product must be kept within a precise temperature range to avoid costly spoilage, and any deviation could result in significant financial losses and damage to the brand's reputation.
The trade route in question included two legs - over land and ocean. Each presented a series of environmental obstacles, from tropical heat to cooler, high-altitude regions, where external temperatures ranged from a sweltering 44°C to a much cooler 7.5°C. The company needed a solution that could maintain an internal temperature threshold of 35°C or lower, ensuring their product remained protected in such diverse climates. The stakes were high—product integrity had to be preserved regardless of the conditions outside.
Real-time monitoring in natively insulated containers
To meet the company’s needs, AELER provided its smart containers equipped with advanced sensors to continuously monitor internal and external conditions, including temperature, humidity, and impact. This real-time data was made available through AELER’s Control Tower, providing full visibility into the interior container condition throughout the journey.
AELER's Unit One containers came equipped with superior native insulation, built directly into the container’s design, allowing them to maintain stable internal conditions despite the often harsh external environment.
For instance, on the land leg of the journey, while external temperatures fluctuated between 21°C and 38°C, internal temperatures stayed within the safe range of 23°C to 34.4°C. During the ocean leg, the internal temperature stayed below 35°C degrees while external temperature reached around 44.2°C.
Additional cargo protection and stability
In addition to managing temperatures, humidity levels inside the container were critical to ensuring the syrup's quality. Despite external humidity reaching a stifling 100%, Unit One maintained internal humidity between 49% and 85%, protecting the cargo from any potential damage. This level of control proved invaluable, keeping the product safe from moisture-related issues.
Furthermore, the cargo faced the constant threat of physical impacts during transport, with the largest recorded shock being a significant 8.48G—likely occurring during truck loading. Yet, thanks to the superior design and durability of AELER’s containers, no damage occurred to the container or its precious contents.
Conclusion: Ensuring reliability every step of the way
By utilising AELER’s cutting-edge smart containers, this major beverage company successfully protected and preserved their product from temperature and humidity fluctuations, ensuring that the internal temperature stayed well within the threshold of 35°C or lower. The real-time monitoring offered through AELER’s Control Tower gave the company unprecedented insight into every aspect of the shipment, from temperature and humidity to security, ensuring complete transparency and control.
With enhanced cargo protection, real-time monitoring, and zero product loss, this company has now set a new benchmark in logistics, paving the way for smarter, more secure transport of temperature-sensitive goods. AELER’s smart containers not only met the challenge, but redefined what’s possible in the world of modern logistics.
Related resources
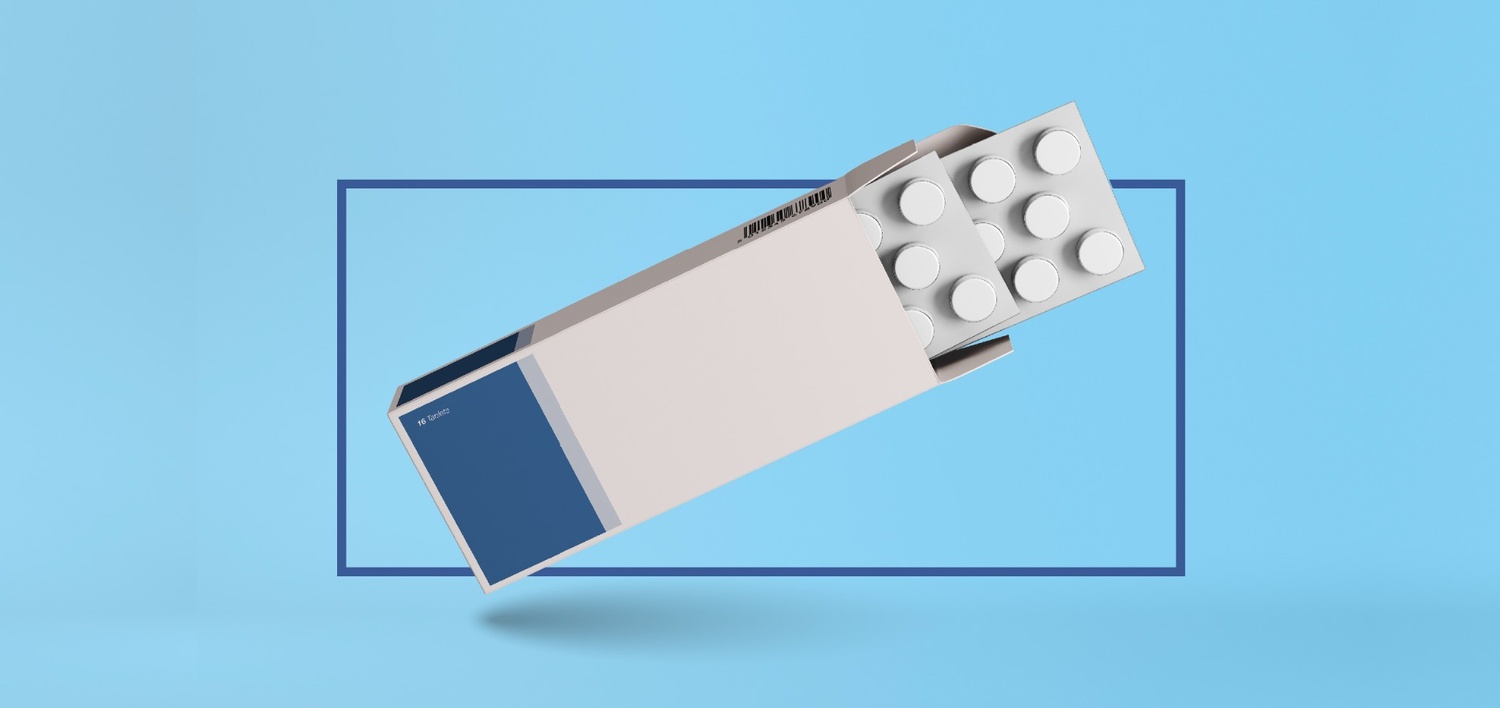
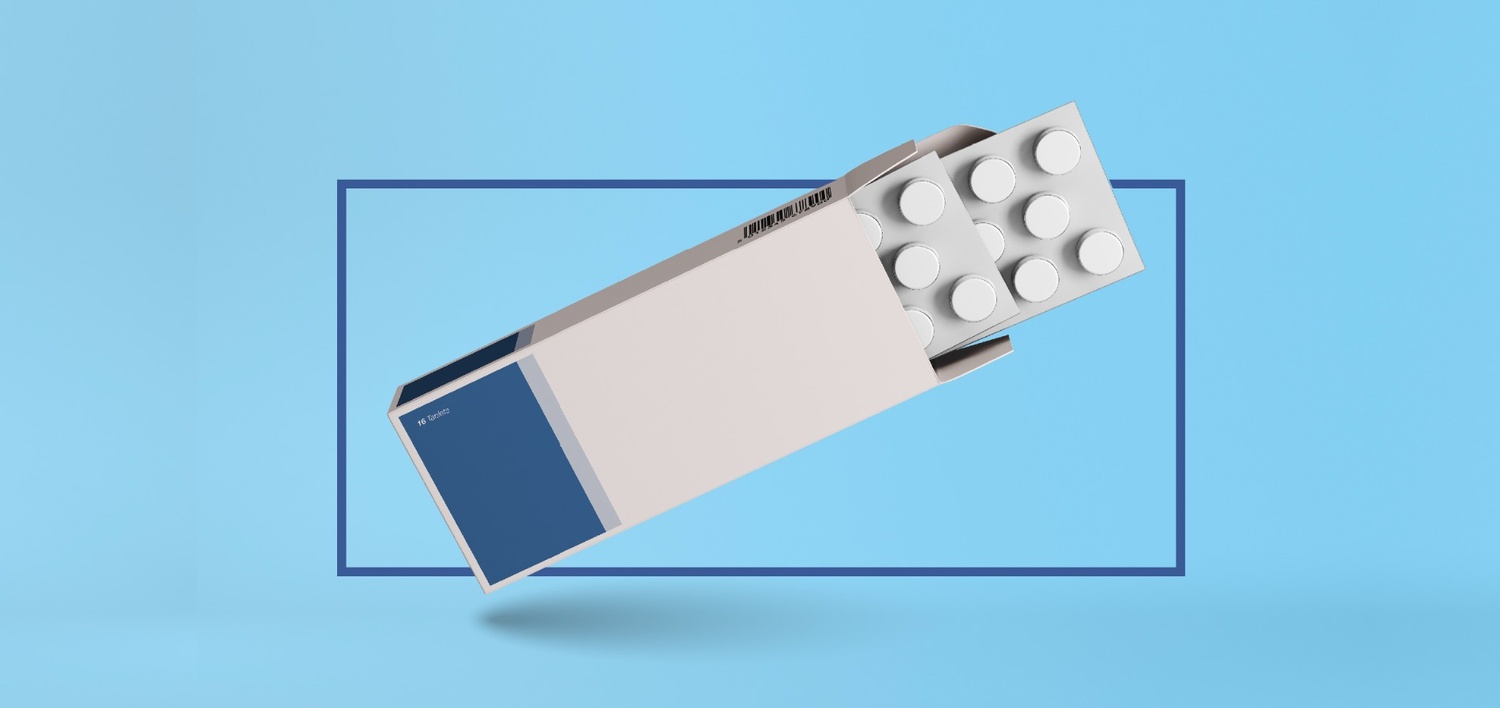
Case study: transforming pharmaceutical logistics with smart containers
Case study: transforming pharmaceutical logistics with smart containers
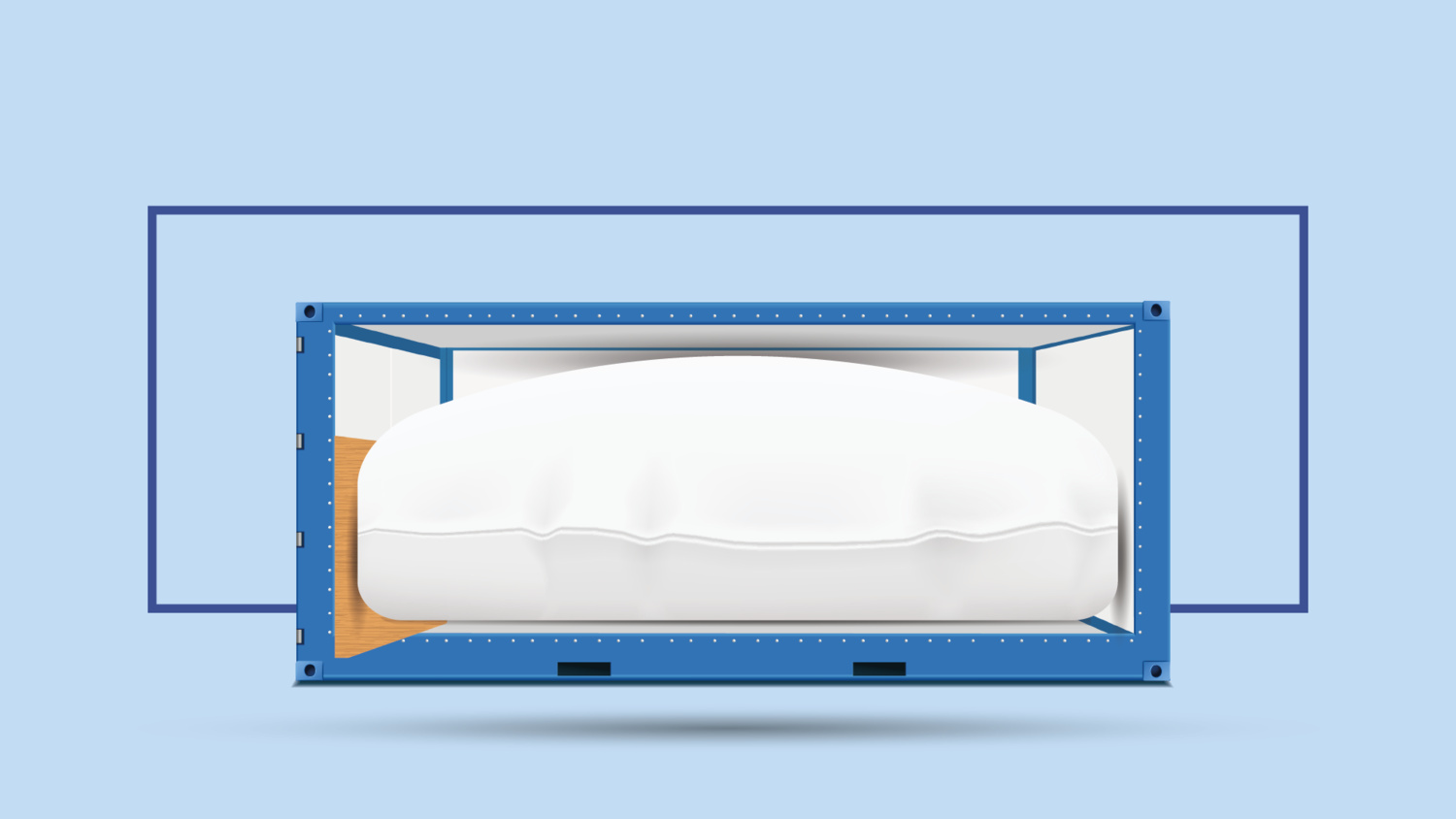
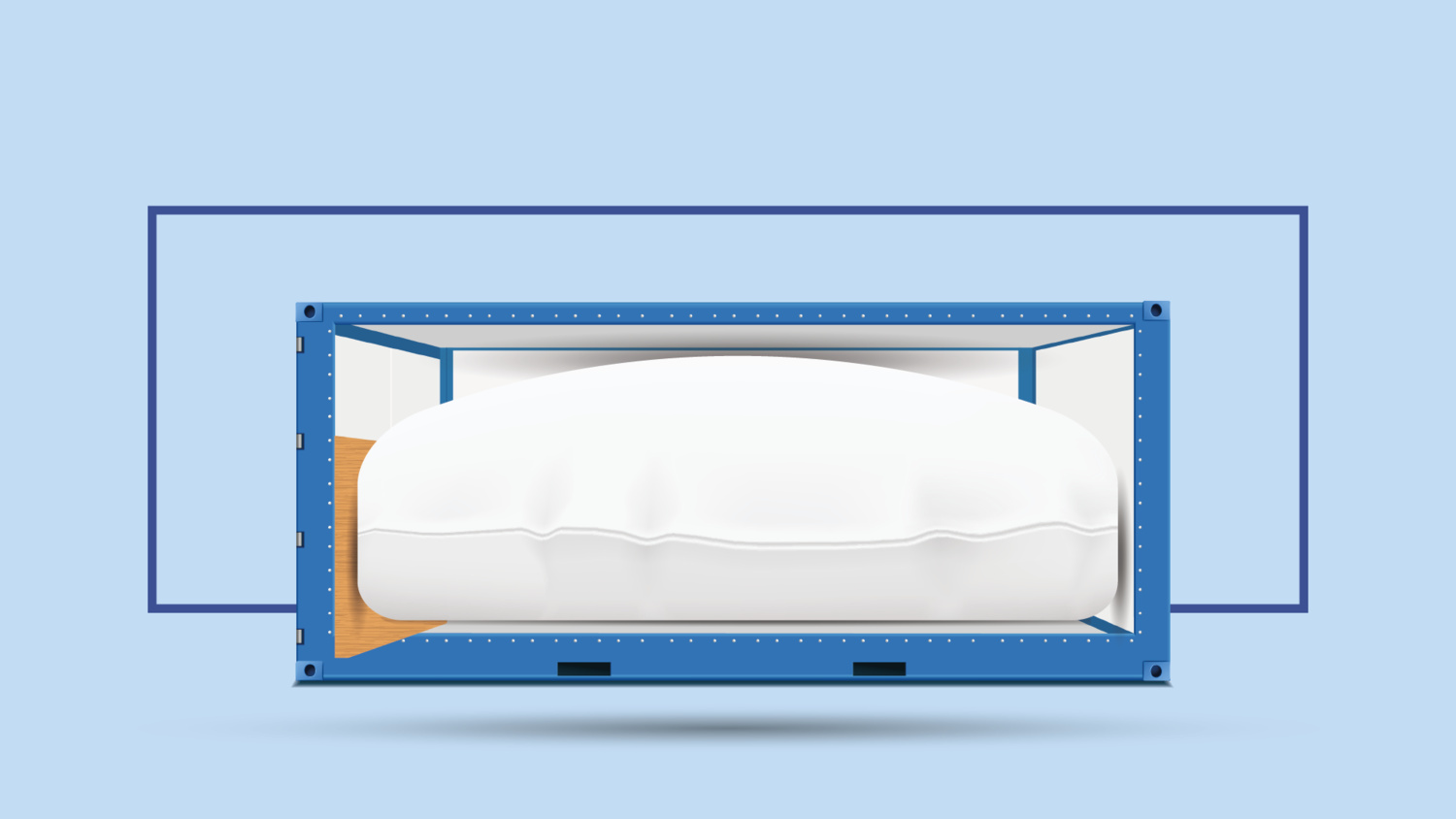
Case study: cutting costs and maximising efficiency in bulk liquid transportation
Case study: cutting costs and maximising efficiency in bulk liquid transportation
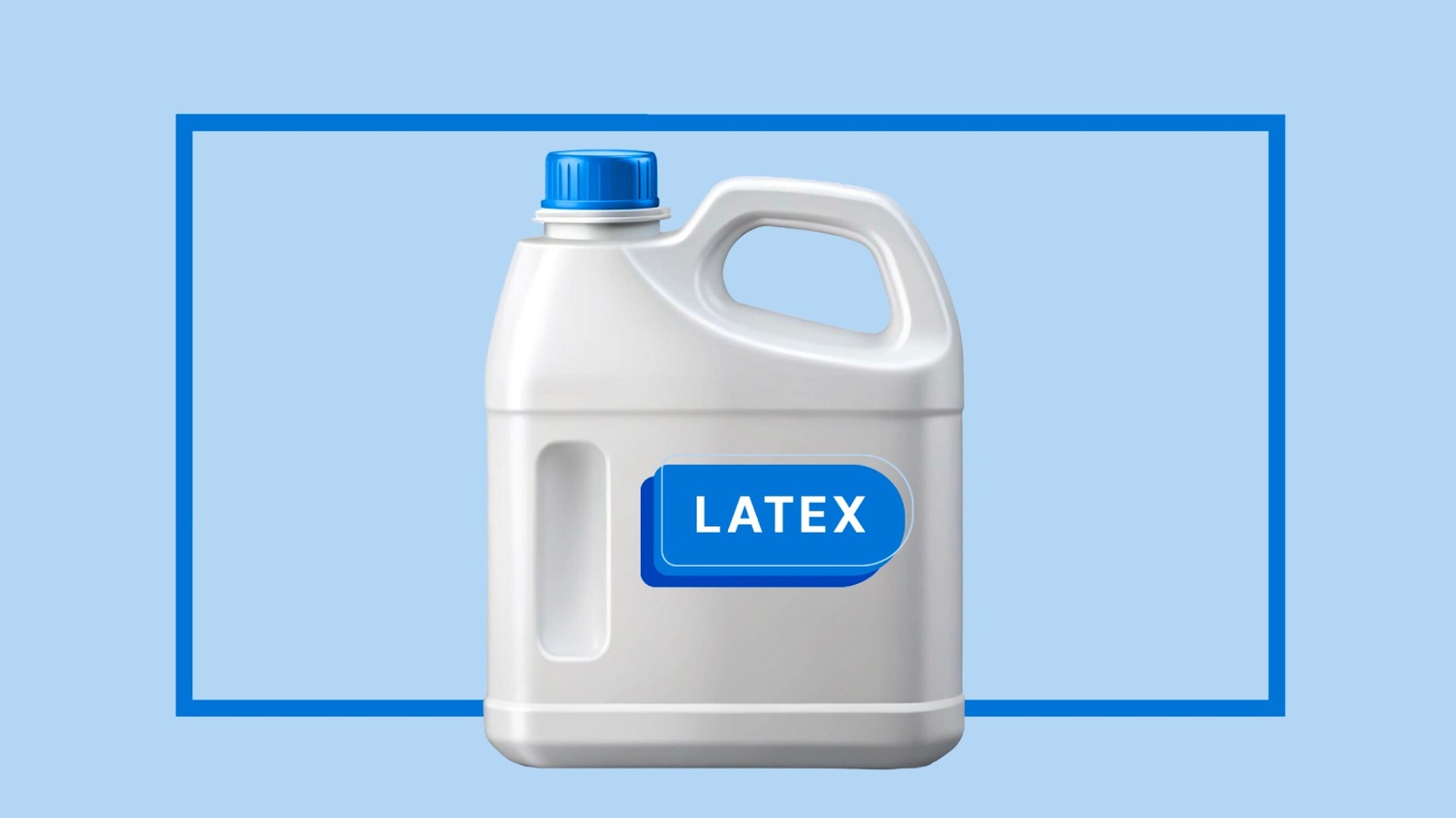
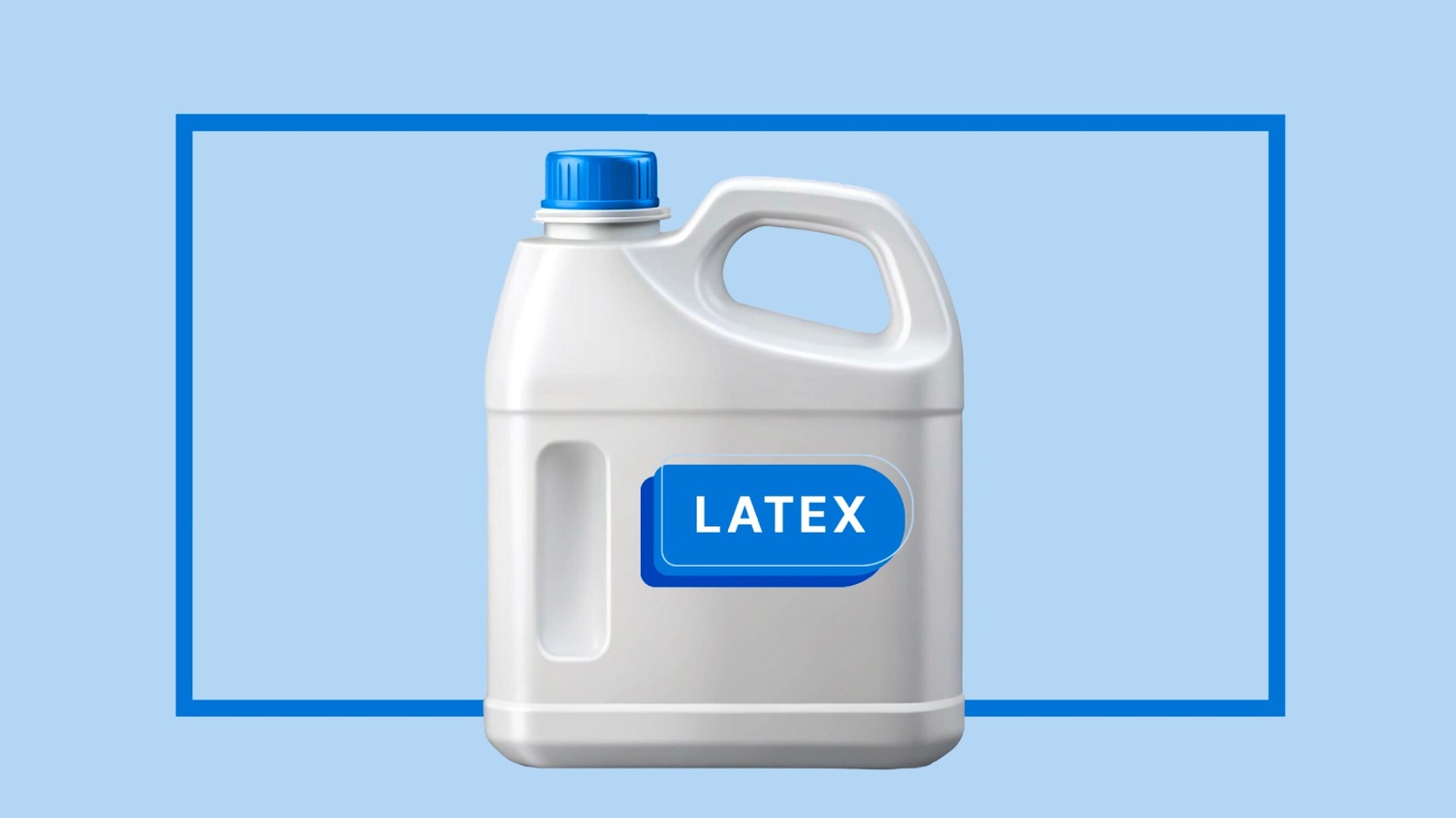